Food Industry Equipment 101: What to Know
Technology has greatly impacted how many businesses are run, and the food industry is no exception. From filling machines to automatic product counting machinery, food industry equipment can make life much easier and production much faster.
If you are looking to streamline your operations, cut costs, and improve the overall quality of the products you deliver, here is what you need to know to get the most out of your food industry equipment.
Why You Must Train Employees on Using Filling Equipment
Efficiency and safety are crucial KPIs for businesses that operate any sort of machinery – food industry equipment included. When it comes to operating packaging or filling equipment, these and other KPIs cannot be achieved without proper employee training.
Insufficient training can result in not only serious safety concerns but also wasted time, money, materials, and parts.
Here are a few reasons why you need to train employees on using filling equipment:
- Improved Efficiency - Well-trained employees will be familiar with the machinery they are required to operate on a daily basis. This means they will feel more confident and equipped to do their jobs, improving employee engagement and productivity while minimizing the potential for costly mistakes. Employees will also be better equipped to spot room for improvement and handle inefficiencies before they lead to delays.
- Higher Levels of Safety - Comprehensive safety standards are a must for any business that uses complex machinery and hopes to avoid serious injuries or even death. In addition to knowing how to operate the machinery safely, well-trained employees are aware of potential safety risks and what steps to avoid. An improperly trained employee operating any machinery poses safety risks not only to the untrained employees but also to those around them.
- You Save Time and Money - If employees who are required to operate machinery are adequately trained, they will be better equipped to maintain high levels of productivity and reduce machine downtime by troubleshooting and addressing potential problems immediately and safely.
Experienced employees will also be able to maintain the machines and conduct regular checks to prevent malfunctions and identify potential issues before they can cause a backlog. Proper machine maintenance and troubleshooting techniques can save your business time and even money that would otherwise be spent on expensive machinery repairs.
Training can reduce accidents, decrease downtime, and equip your staff with the skills needed to deal with problems proactively.
Should You Invest in a Product Counting Machine?

Product counting machines (production counters) are designed for the high-speed and accurate counting of products and packages of different shapes and sizes. While their primary purpose is tracking the number of products produced or packages on a production line, they are also useful in driving improvements in manufacturing productivity (among other benefits).
If you run a business in the packaging industry, there are quite a few ways you could benefit from investing in a product counting machine.
- Boosts Customer Satisfaction - Automatic production counters can help you achieve 100% packaging accuracy so you can be sure that each customer is receiving the correct order, improving your customer satisfaction and, therefore, your customer retention rate.
- You Save Time and Money - Automation is meant to mitigate the bottlenecks caused by manual practices. Product counting machines are easy to dismantle (and typically don’t require any tools to do so). They are also easy to clean, which is essential for food hygiene in manufacturing. These are both safety and productivity benefits. You are ensuring hygiene and efficient product maintenance while also reducing machine downtime.
In addition, automatic counting machines are a lot faster and more accurate than manual counting systems – saving you time and allowing you to save on hiring expenses, salaries, and other labor costs.
- Minimize Waste and Improve Accuracy – A well-designed counting machine will preserve the shape and texture of the products, regardless of whether you are packaging wet, fragile, or dry produce.
This accuracy reduces production rejects and waste while also supplying a unique selling point to customers who purchase in bulk and are more concerned with “how many” as opposed to “how much.” This transparency and convenience is especially useful to customers in industries like event planning or catering. For example, if they can see that 50 chicken wings are in a package (instead of just the weight), they know exactly how many packages to buy for their event.
- Versatility – Weight machines are tall, noisy, and take up a lot of room in the production facility. A counting machine, on the other hand, operates quietly and is compact enough to seamlessly integrate with your existing systems and free up the valuable space needed to support extensive production lines.
Every manufacturer needs an accurate count of what they produce, but far more than tracking the number of products packed, counting machines can also be used to drive significant improvements in manufacturing productivity when combined with production monitors.
With the same sensors used for counting parts, you can generate dozens of meaningful and insightful metrics that provide a comprehensive view of your manufacturing processes. In addition to giving you insight into production counting (total count and good count), production monitoring features can give you insight into cycle times, rates, production times, targets, Overall Equipment Effectiveness (OEE), the Six Big Losses, and Total Effective Equipment Performance (TEEP).
Centrifugal Machine vs. Cellular Tray Machine
Automated, high-speed counting machines simplify and streamline the production process – provided you are using the correct type of production counting equipment. Two commonly used types of high-speed counting machines are centrifugal machines and cellular tray machines. The question is, which is better for your business?
A
cellular tray counting machine
takes a large number of products and distributes them evenly into specially designed trays. These machines use a release hopper to distribute bulk products in an orderly fashion and operate in unit distribution, products released on-the-fly, or in batch distribution. The machines will have interchangeable trays, depending on the product size, and are able to count products with care and complete accuracy.
Cellular tray machinery is typically installed upstream of your main packaging system and downstream of your freezer, freezing tunnel, or oven. Cellular tray machines can be used to count:
- Sweet food products (candy, bubble gum, fruit pieces, chocolate)
- Savory products (onions, tomatoes, olives)
- Frozen products
The products can then be distributed, counted, or batched individually (or grouped together) to be loaded or packaged.
A
centrifugal counting machine
uses centrifugal force to align a large number of disordered products at high speed and in a continuous, ordered flow. These machines were designed for minimal waste, as well as accurate and safe product counting. In most cases, centrifugal machines are installed upstream of your primary packaging system and downstream of your freezer or oven.
These machines can be used to count bakery products, meat products, animal treats, cubed broths, dry food products, candy, bubblegum, and more. After counting, depending on your application, the products can then be either distributed or batched (independently or together) to be loaded into your horizontal bagger, vertical bagger, trays, pots, cans, etc.
Both machines are designed to maximize your OEE by accurately counting bulk products at high speeds while minimizing damage, waste, and production rejects. Fragile, wet, or dry products can be counted without compromising their quality, shape, or texture.
Why Should You Automatize Your Filling Systems?
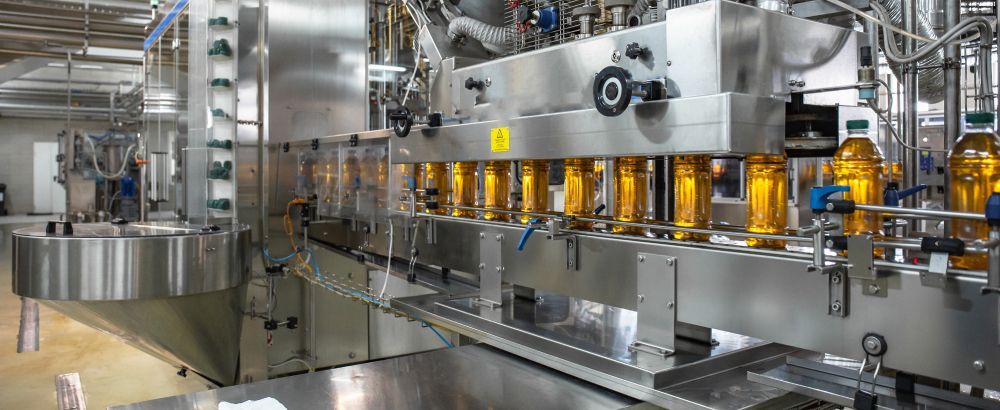
Globally, food processing companies undergo extensive scrutiny by their respective governing bodies. Along with regulatory compliance, you must also find a balance between consumer demands and business productivity and profitability. This is why automation is so helpful. In addition to minimizing human error, improving client satisfaction, and increasing insight into your business, there are numerous ways that automating your filling system could be beneficial to your business.
- Consistency - Automatic filling machines ensure consistent, repeatable, and reliable fillings with each cycle, regardless of what measurements are used (level, weight, item count, volume, or other measurements).
- Speed - Filling bottles Automation has a significant impact on your packaging speed. Automatic filling machines allow packagers to fill more containers in a shorter amount of time than they would if they were using a manual filling process.
- Opens up room for expansion - Determining scalability in business can be complicated. There are several variables that need to be taken into account, operating costs being one of them, which is why manual processes often stand in the way of expansion. However, by automating your processes, you simply have to make sure that your systems can accommodate the growth. If they can’t, this is usually fixed with a minor upgrade.
- Versatility - Automatic filling machines don’t need to be used for one single container or even one type of product; they can be set up to handle a range of container sizes and shapes. In addition, many machines can handle multiple products, which is helpful for companies that package an array of products in various containers.
- You can keep operating during a tight labor market - Automated filling machines allow for containers to be filled faster and more accurately than manual filling processes. This not only reduces wastage and human error, but it allows you to redeploy your current staff into tasks that actually need manual intervention. You can, therefore, improve your resource utilization and business productivity without the need for additional staff. Plus, your existing workers will get an opportunity to learn a new skill and contribute to a different process within the production line.
How AI Can Assist in the Food Industry
Businesses in the food and beverage industry are under constant pressure to evolve in order to meet the growing global demand while still balancing their efforts to increase profits in an increasingly hypercompetitive landscape.
Leveraging Artificial Intelligence (AI) is one of the best ways to cut costs, identify bottlenecks, and proactively address issues caused by manual processes.
Supply chain management can be improved with accurate insights into inventory management and pricing, helping to ensure profitability and avoid unnecessary costs.
AI can help achieve
better hygiene management and reduce the chances of food safety breaches or cross-contamination. Automated machines are designed to be easy to clean, but in addition, the fewer parts of the production process that are handled by humans, the less likely products are to be contaminated. There are also some AI solutions that use sensors or fluorescence imaging to scan food remains on the machinery after use so workers will know exactly where to clean.
AI can also
analyze energy consumption and waste, helping you conserve valuable resources and saving your business money. You can use the insights provided by AI to keep your energy usage at an optimal level and ensure energy is only being consumed in an on-demand basis. Automated filling and counting systems perform their functions with extreme accuracy and care as well, so you are minimizing damage, waste, and production rejects.
These are just a few of the ways automating manual tasks allows companies to bring down their labor expenses, reduce downtime, and speed up the production process. AI is revolutionizing the food processing industry and will likely continue to transform this sector in the future.
The Importance of Counting Machines for Hygiene
Hygiene is essential in the food and beverage industry; it is not only a legal prerequisite but is essential in maintaining product quality and preserving your reputation. You need to ensure that, when you are counting food products, you are leaving no room for cross-contamination (which is an allergy risk) or contamination from germs, pathogens, and bacteria.
Proper hygiene and sanitation measures should be the cornerstone of all of your operations. This is why it is important to look for filling and counting machines that have been designed with hygiene in mind. For example, MULTI-FILL has partnered with Velec Systems for its complete suite of food processing equipment. The counters are designed to make maintenance and cleaning operations easy and simple. They are easy to dismantle, making cleaning simple and more effective.
MULTI-FILL’s filling machines were designed with the same hygiene priorities in mind. They offer easy cleaning to a microbiological level, materials that are easy to clean, hermetically sealed hollow areas, exclusion of any niches where food debris can collect or bacteria could grow, and so many more design features that facilitate cleaning and sanitizing protocols.
MULTI-FILL Inc. is recognized as a leader in high-quality food-filling solutions for difficult-to-fill products. Our fillers can be found on the majority of ready-meal lines for major players in the prepared food industry, as well as smaller customers. For decades, we have provided volumetric filling solutions to satisfied customers all over the globe.
Contact us today to learn more about our products and how we can assist you.
Designing a food filling line: Product is king
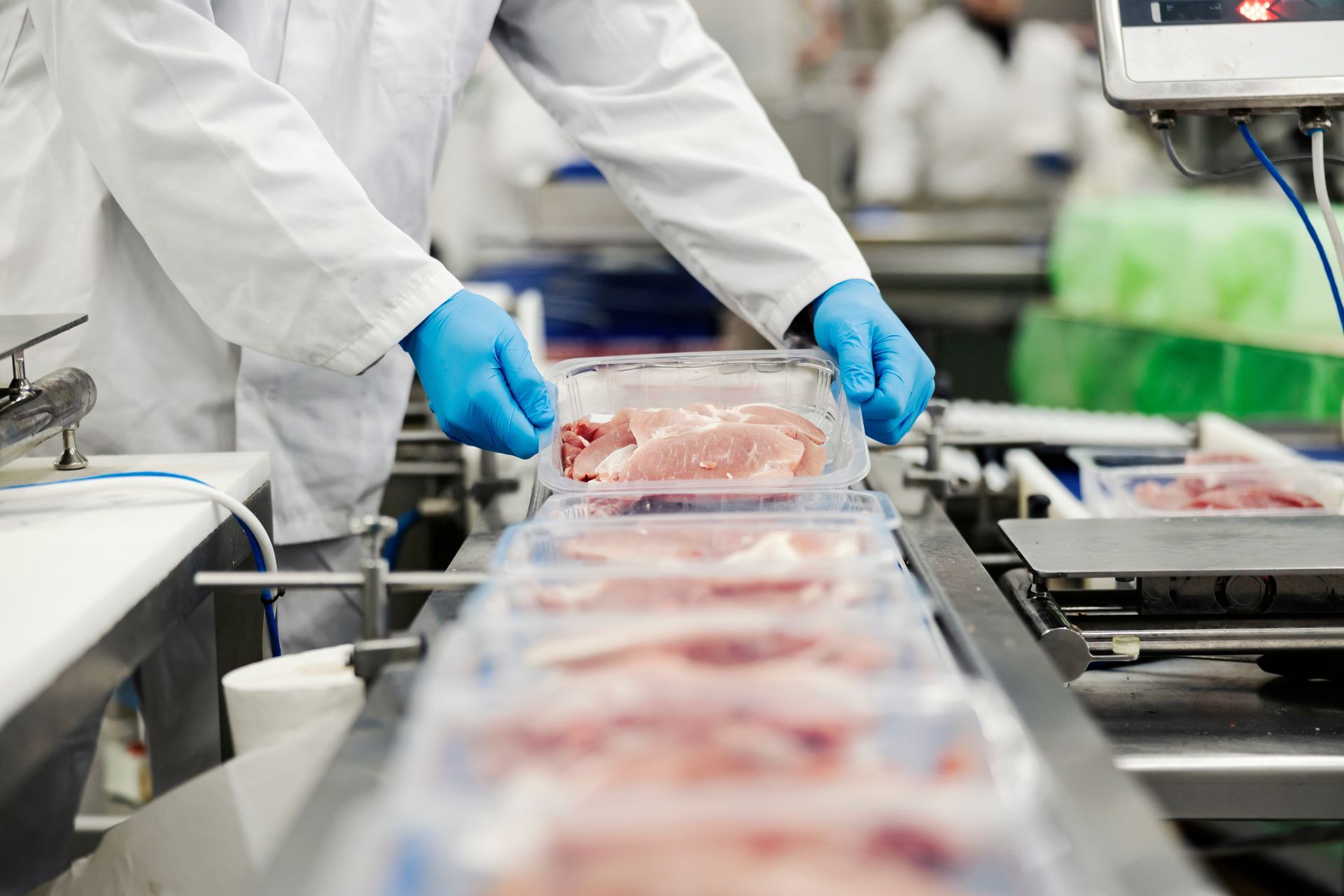
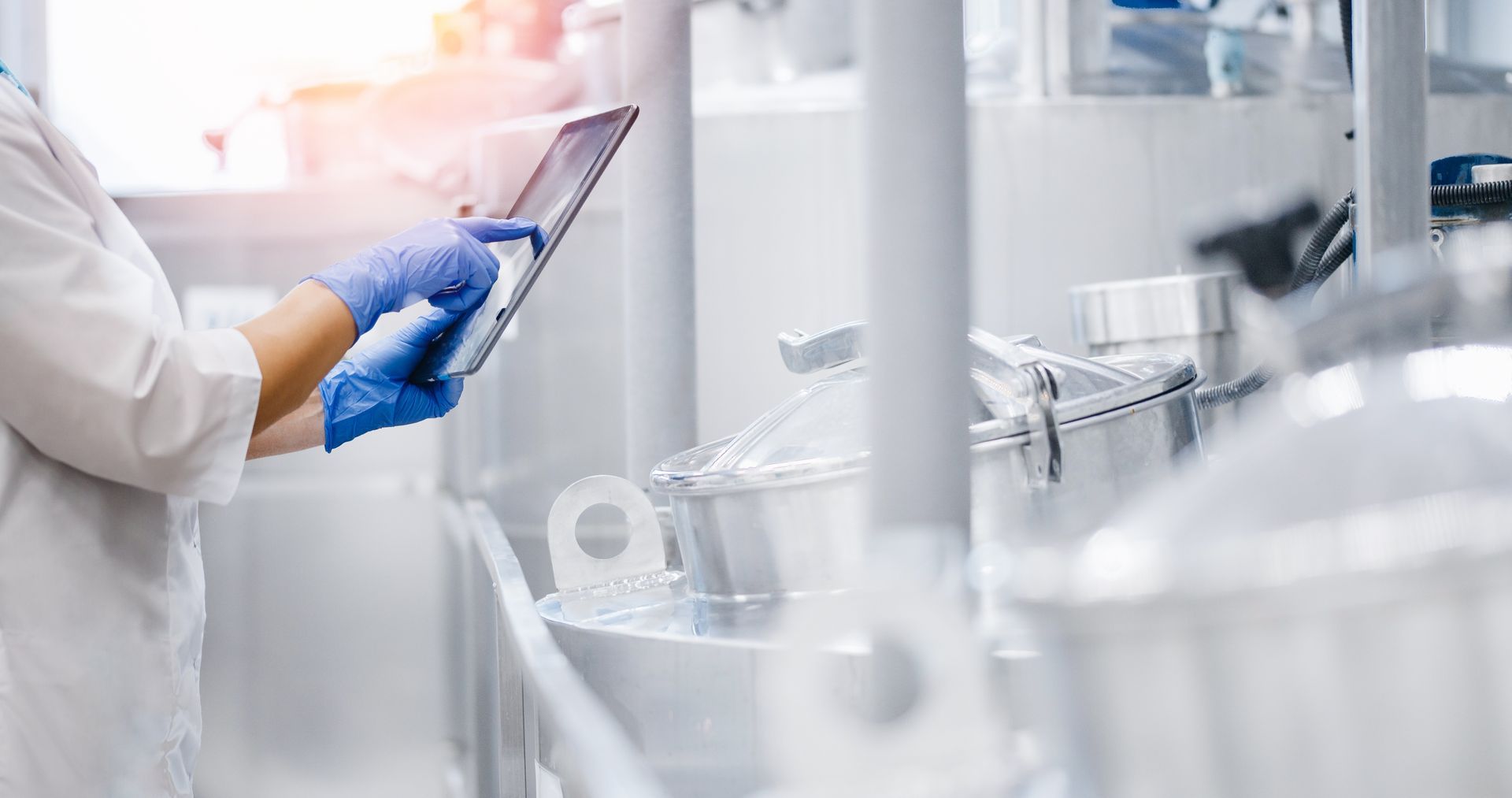
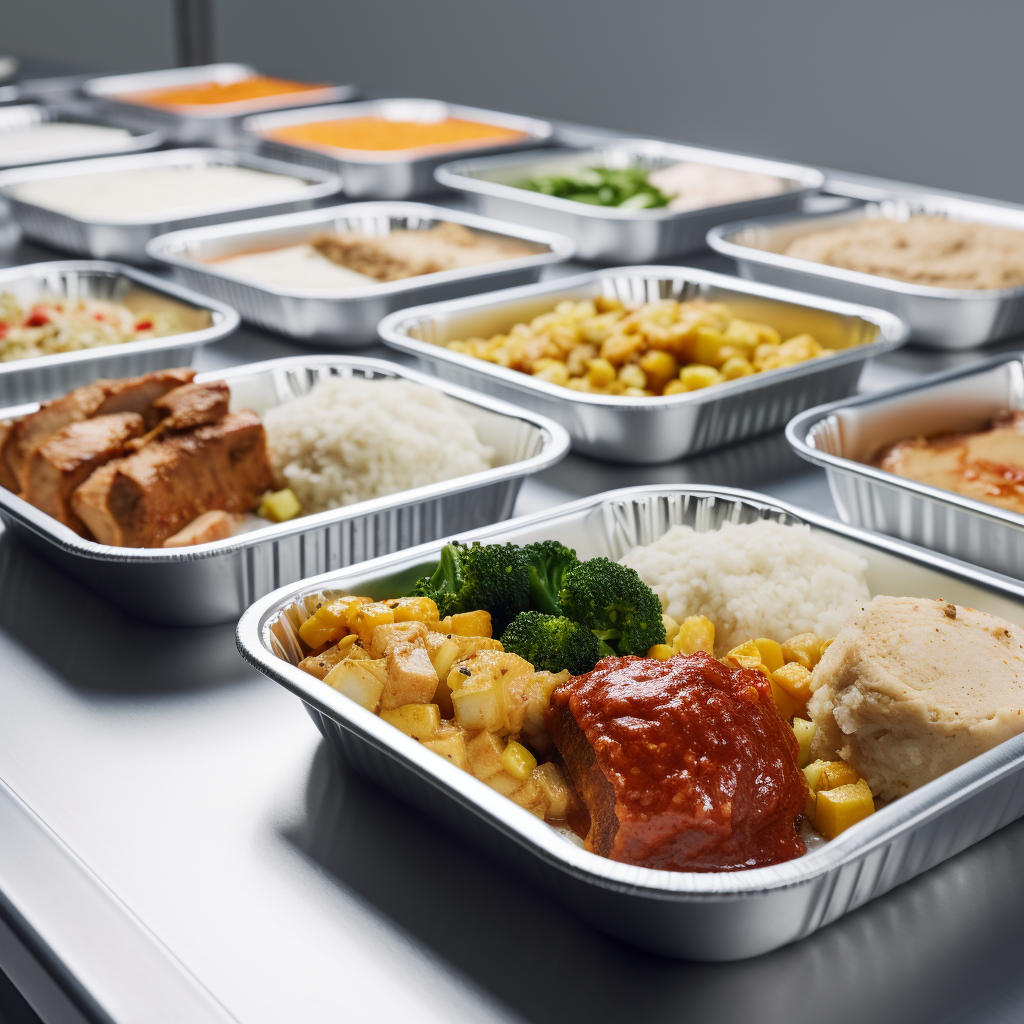