Michael Naylor • July 10, 2020
Food Filling Machines for Soft Grainy Foods
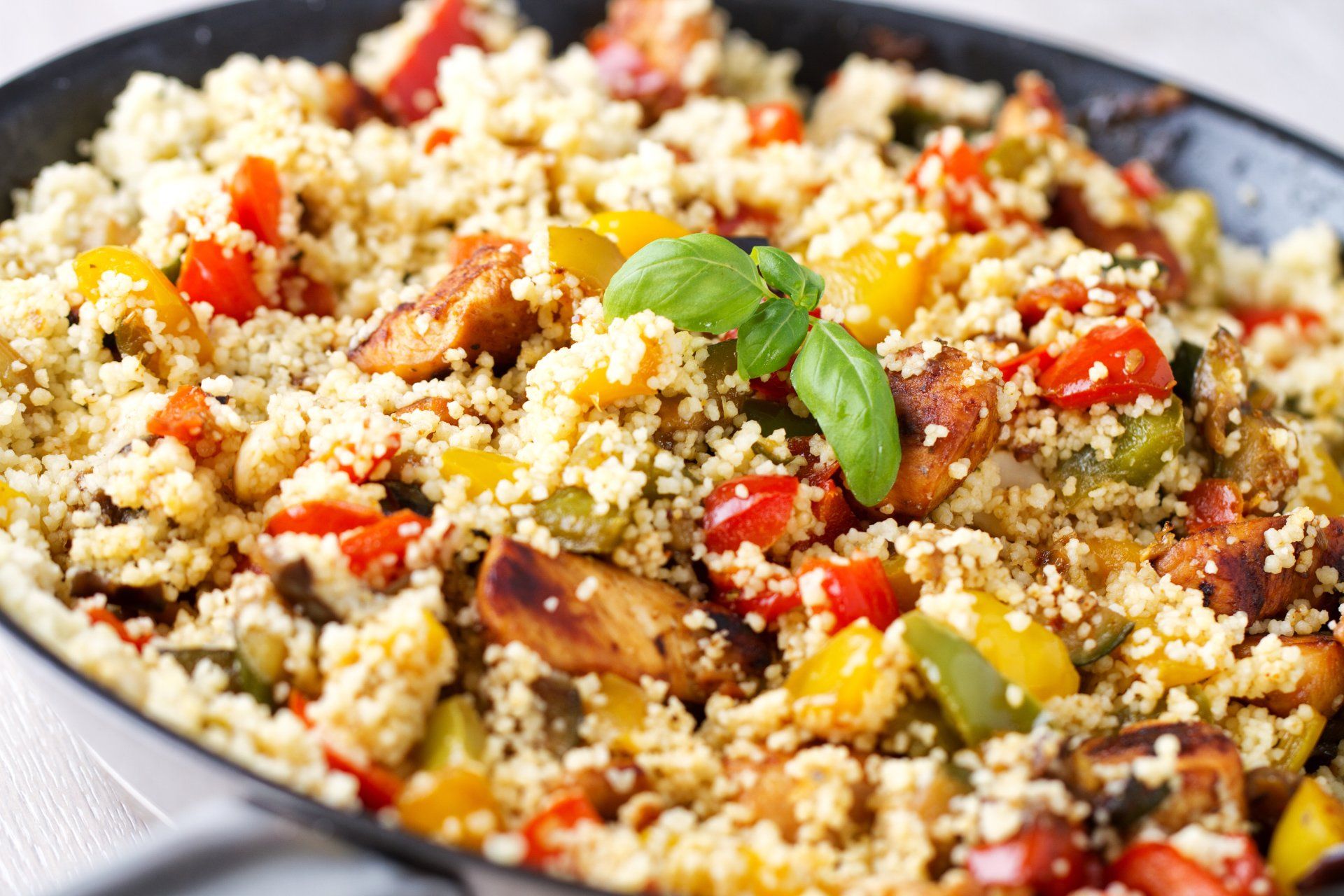
The demand for healthy ready to eat meals like couscous and quinoa is steadily gaining in popularity. Cooked rice, of course, has long been a staple in packaged meals. Making the choice of a food filling machine for these soft grainy foods is important for producers to deliver a positive customer experience.
We’ll focus on couscous as an example, but the points covered below apply to all foods of similar size and texture.
The main challenge the ready to eat food industry faces when working with couscous is its tendency to stick to the inner walls and compartments of the food depositor. In order to fill each serving equally and efficiently, the machine must be able to ensure the smooth volumetric flow of soft grainy foods from production to final packaging.
The machine must also feature ease of sanitation so that the insides can be quickly cleaned between operating shifts, or in accordance with health and safety standards. To this end, it is essential that food producers choose filling machines made from sanitary materials such as 316 stainless steel and food-grade polymers.
As a producer, your best option for couscous, quinoa, and cooked rice is a volumetric filling machine. Unlike pumps, which are designed primarily for liquids, volumetric fillers can be custom-made to handle soft grainy foods.
Multi-Fill’s MPFSC-120 Automatic Pocket Filler
is the ideal choice for soft grainy foods. It can keep each part of a packaged meal separate while sustaining a rapid output. Here’s an overview of its features and functions:
Contact us today to learn more about cooked rice food filling machines and food depositors. Call us at 801-280-1570 or reach us online.
Keeping Meals Attractive from Food Depositor to Packaging
Multi-Fill has the Right Volumetric Filler for You
- Dispenses clean, accurate portions
for a wide variety of difficult-to-fill products:
- Measure perfect portions of couscous, quinoa, cooked rice
- No-mess filling for cooked pasta, cut vegetables, cut fruit, refrigerated salads, cereal, trail mix
- Rated at speeds up to 120 containers per minute
- Compatible
with a wide variety of container conveying systems:
- Suits a range of packaging options—trays, plates, cartons, cups, pouches, cans, jars, boxes, and more
And here’s what sets the MPFSC-120 apart from the competition:
- Lowest total cost of ownership of many machines over the production lines.
- Flexibility of the filler both in terms of containers, products, or conveyor lines (intermittent or continuous motion).
- Sturdiness of the machine and upgrade ability of the filler.
- Reliability and consistency of filling with an automatic filling machine.
Contact us today to learn more about cooked rice food filling machines and food depositors. Call us at 801-280-1570 or reach us online.
Designing a food filling line: Product is king
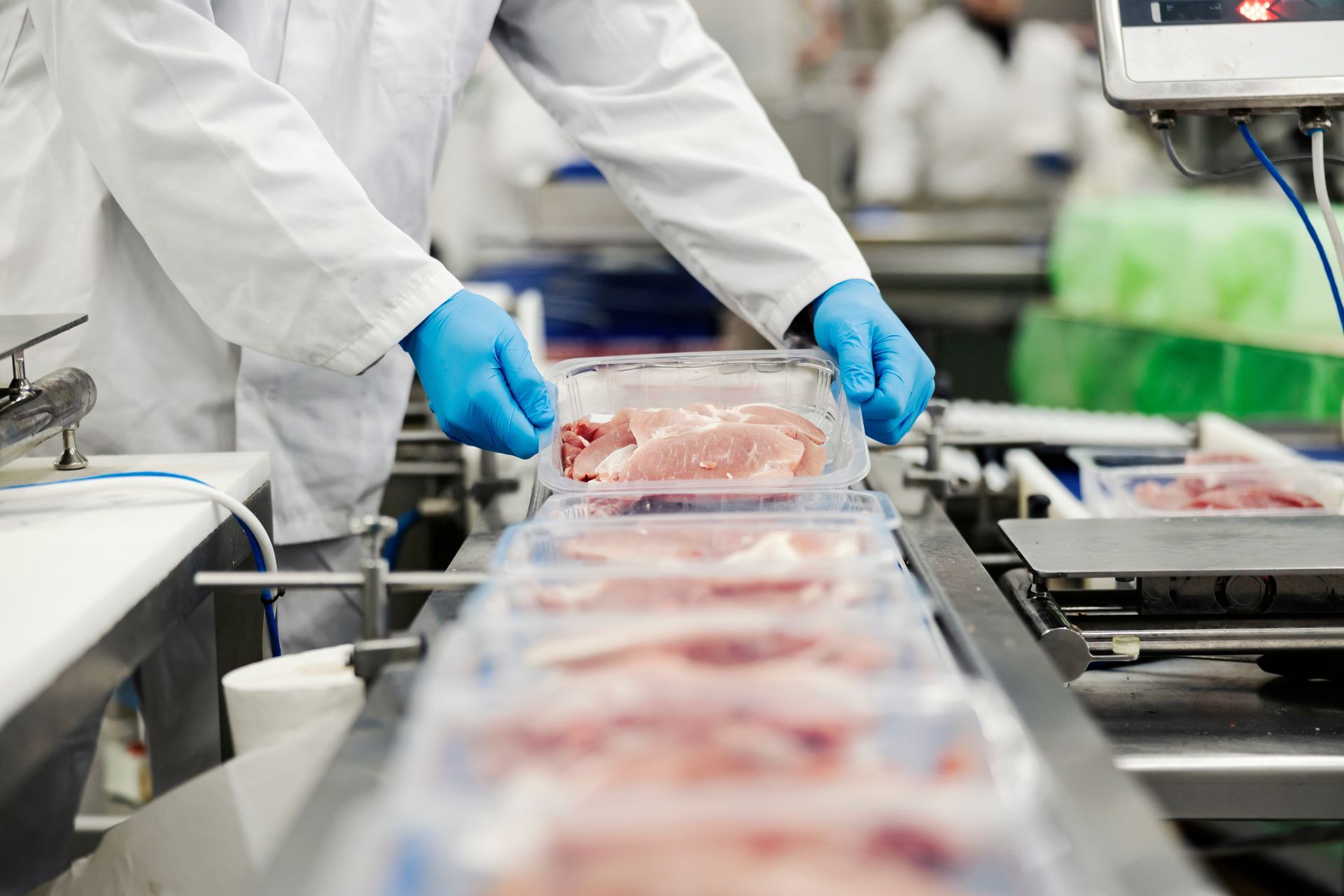
Food packaging plays a vital role in ensuring the safety and quality of the food we consume. To maintain high standards and prevent foodborne illnesses, the food packaging industry follows a set of regulations known as Current Good Manufacturing Practices (cGMP). In this article, we will delve into cGMP and explore its impact on preventing foodborne illness. We will also take an inside look at how cGMP is implemented on a food factory line, the role of food filling equipment in ensuring compliance, and discuss the future of cGMP in food packaging for strengthening food safety.
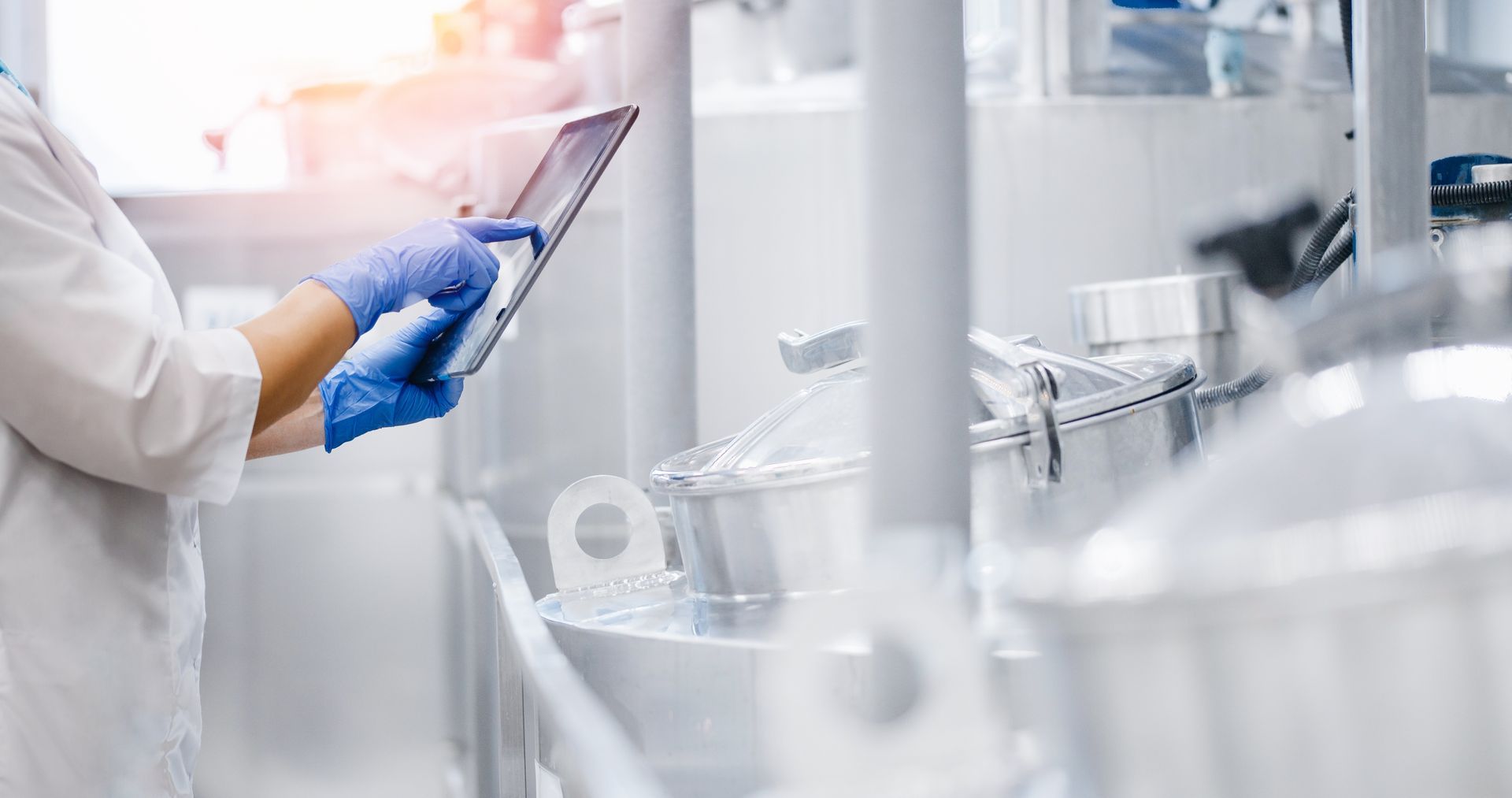
Current Good Manufacturing Practices Food safety is of utmost importance in the food industry, and several systems work together to prevent foodborne illnesses. This article explores the harmonization of Current Good Manufacturing Practices (cGMP), Hazard Analysis and Critical Control Points (HACCP), and Hazard Analysis and Risk-based Preventive Controls (HARPC) in ensuring food line safety. We will delve into the synergy between these systems, the role of critical control points, and their practical application in both automatic and manual counting devices. Additionally, we will discuss how cGMP, HACCP, and HARPC optimize automatic filling machines for enhanced food safety. This article is in our series on Current Good Manufacturing Practices. Read the first article here.
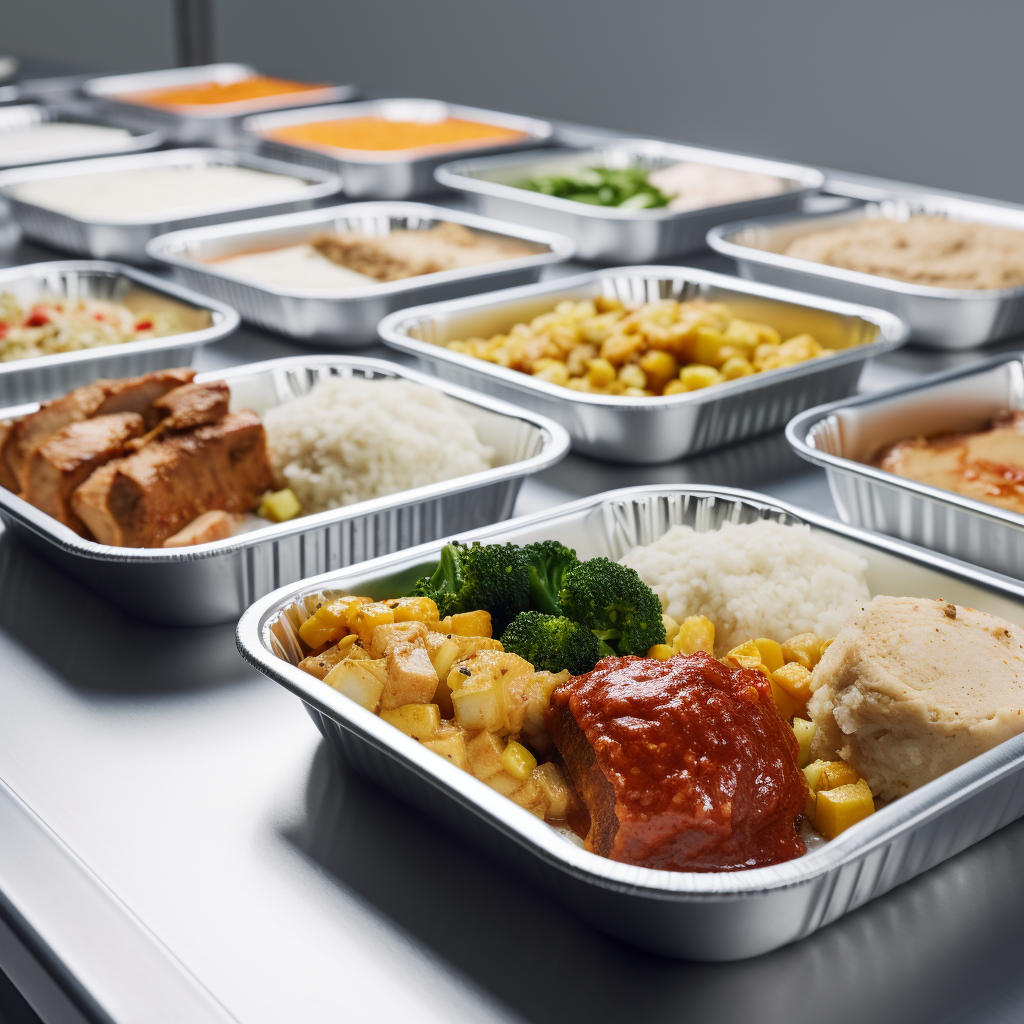
In this article, we explore the crucial role of Current Good Manufacturing Practices (cGMP) in ensuring food safety and preventing foodborne illnesses. We'll delve into the significance of hazard analysis and critical control points (HACCP) and how they contribute to mitigating risks. Additionally, we'll discuss the role of Hazard Analysis and Risk-based Preventative Controls (HARPC) in enhancing food safety measures. This is the first in a series of articles on Good Manufacturing Processes in Food Processing. In this article: Understanding the Importance of cGMP in Food Packaging How Hazard Analysis and Critical Control Points (HACCP) Prevent Foodborne Illness The Role of Hazard Analysis and Risk-based Preventative Controls (HARPC) in Food Safety Critical Control Points in Food Packaging The Intersection of cGMP, HACCP, and HARPC in Food Safety