Michael Naylor • July 10, 2020
Multi-Fill in the News
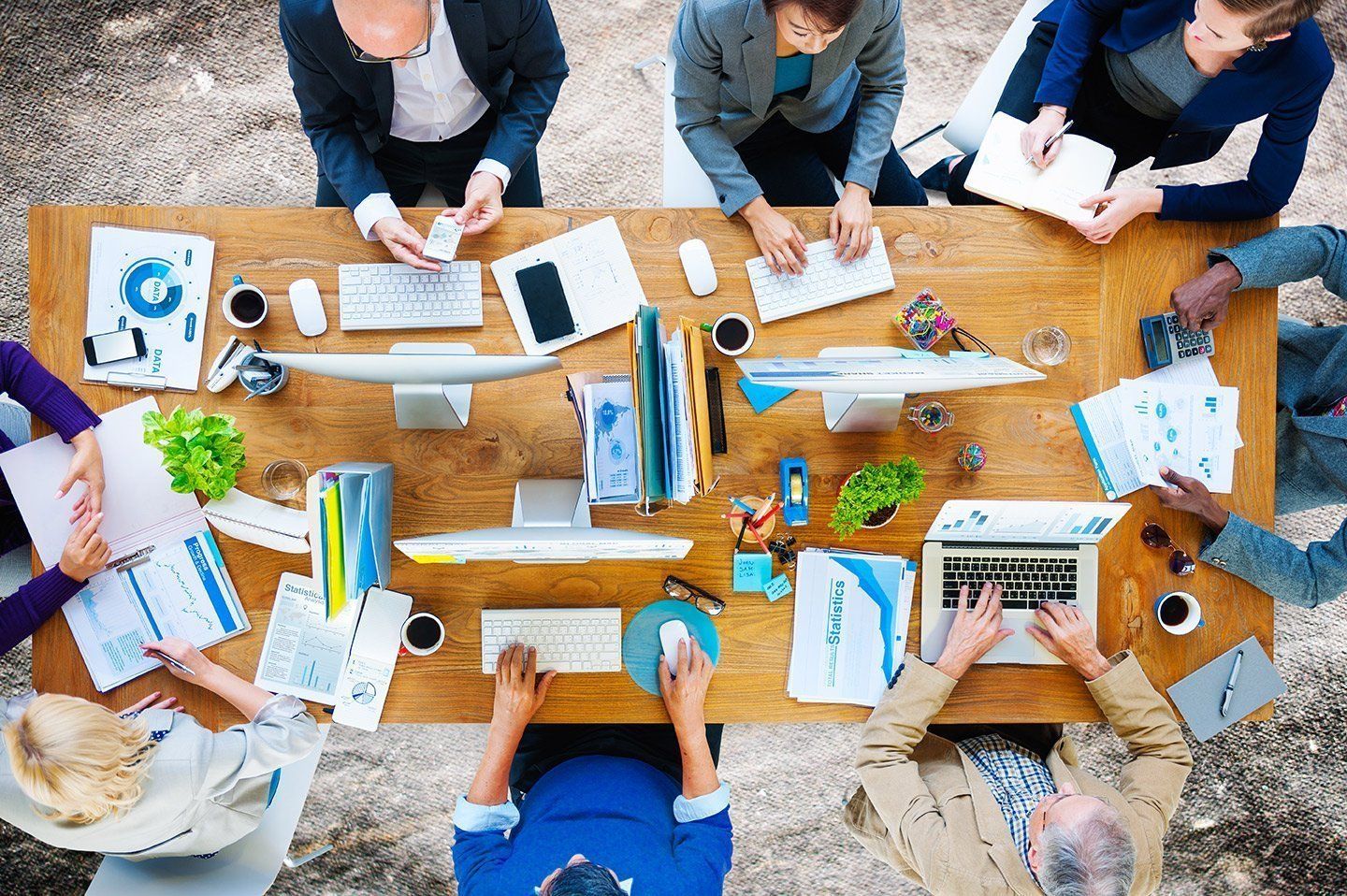
We've been leading the the volumetric food filling industry for decades and have earned a reputation we're proud of. Quality, efficiency, safety, and cleanliness are all areas we excel in through continually evaluating our designs and developing innovative improvements to the technology, in order to meet the unique demands of each customer and production line.
But you don't have to take our word for it. Here are just some of the things the news has said about us over the years, from around the world.
- La MPF, une doseuse volumétrique pour les produits difficiles
(Agro Media, January 2017)
Ces machines sont idéales pour les lignes de production de plats préparés ou produits frais
- Batch feeder reduces manual labor
(Refrigerated & Frozen Foods, September 2016)
MULTI-FILL offers a batch feeder to complement the MPF
- Batch feeder for small goods
(ProFood World, September 2016)
Unit offers multiple feeding options
- Redesigned filling head offers increased efficiency for meals
(Machinery Update, July 2016)
MULTI-FILL has redesigned its MPF filling head to increase efficiency in depositing ready meal components such as cooked long and short pastas, all types of rice, cut fruits and vegetables, prepared salads, and protein pieces
- Sistemas de llenado, distribución y alimentación para resolver sus desafíos de procesamiento
(El Empaque + Conversion, Mayo 2016)
MULTI-FILL ofrece materiales de llenadoras, sistemas de distribución y los alimentadores de lotes para una variedad de alimentos
- MULTI-FILL redesigns filling head
(Produce Processing, May 2016)
MULTI-FILL has redesigned its MPF filling head to increase efficiency in depositing ready meal components
- Réduire ses coûtsgrâce au dosage volumétrique
(Process Alimentaire, Avril 2016)
Maillon essential des lignes de production alimentaires, le dosage gagne toujours en précision, en nettoyabilité et en polyvalence
- Innovaciones en Pack-Expo Las Vegas 2015: apuesta tecnológica segura
(El Empaque + Conversion, Octubre 2015)
Multi-Fill Inc. presentó un sistems de distribución de cuatro posiciones junto con una llenadora volumétrica y un alimentador de alta capacidad
- Fresh Fodder speeds up salad production with MULTI-FILL
(HBM.com.au, August 2015)
MPFMP-060 model volumetric filler increases speed and efficiency of Fresh Fodder salad production line
- MULTI-FILL: volumetric fillers and distribution systems
(Packaging World, July 2015)
See it at Pack Expo Las Vegas Booth #C-2736
- Batch feeding brings benefits
(Machinery Update, May/June 2014)
A new batch feeding system has been developed by MULTI-FILL to allow products to be continuously fed to its MPF automatic volumetric depositors
- MULTI-FILL: batch feeder system
(Packaging World, April 2014)
MULTI-FILL's batch feeder provides a metered, continuous flow of bulk products like cooked pastas and rice, cut vegetables, fruits, meats, and various salads to the hopper of its volumetric cup filler, allowing large quantities to be placed into the hopper with minimal monitoring
- MULTI-FILL presents new batch feeder system
(Packaging Europe, March 2014)
Well known for the high quality, low maintenance, and highly performing filling systems worldwide, MULTI-FILL is adding a batch feeder to its line of equipment
- MULTI-FILL's new batch feeder system
(PMT Direct, March 2014)
MULTI-FILL is adding a batch feeder to its line of equipment
- MULTI-FILL volumetric depositors
(FMCG, November 2012)
MULTI-FILL designs and builds a range of volumetric depositors, named MPF, for products which have previously proved very difficult to fill by machine
- Volumetric depositors offer multi-use options
(Machinery Update, September 2012)
The MPF is aimed at ready meals manufacturers and is designed to handle hard to fill products
- Machines must deliver first class appearance
(Machinery Update, May/June 2012)
The MPF depositor from MULTI-FILL deposits precise portions of ready meal components into trays, cartons or pouches
- Expanded expectations
(Food Engineering, August 2011)
Faster fill times are nice, but a host of other considerations also are part of manufacturers' value calculations. Those needs are evident in the systems being developed.
- Filling roundtable: developments and advice
(Food and Beverage Packaging, August 2011)
Industry experts share insights into automation developments as well as ways to improve your filling operations
- Contents under pressure
(Food Manufacturing, January/February 2011)
Ohio-based Sandridge Food Corporation made a bold $5 million investment in high pressure processing technology, which not only brought the family-owned company into the upper echelon of food safety but also paved the way for the launch of a more natural product line that's delighting its customers across the country
- Depositor suits pasta and rice
(Machinery Update, January 2011)
MULTI-FILL volumetric fillers are ideal for pasta, rice
- Reduce cost, stay flexible
(Refrigerated and Frozen Foods, October 2010)
MULTI-FILL's new filler helps processors reduce cost, add flexibility in multi-lane conveying and packaging lines
- Casa Della Pasta increases output with MULTI-FILL automatic volumetric filler
(Ferrett.com, September 2010)
MULTI-FILL Inc. of Utah, USA, has successfully installed an automatic volumetric filler for a large Victorian food manufacturer,Casa Della Pasta at their Thomastown facility
- MULTI-FILL depositors for ready meal components
(Packaging International, January 2010)
MULTI-FILL Inc. design and build a range of depositors, named MPF, for products which have previously proved very difficult to fill by machine
- Efficiency and the recipes for success
(Machinery Update, March/April 2009)
Discussing the successful installation of volumetric filling equipment for cooked, chilled rice and spaghetti at Headland Foods (UK)
- Marsan Food bringing winning food ideas to your table
(Canadian Business Journal, March 2009)
Chosen as one of Canada's 50 Best Managed Food Companies for the fourth year in a row, Marsan Foods Limited has enjoyed recognition as a leading producer of high quality food products
- Frozen entree producer installs high-efficiency casing equipment
(Packaging World, November 2008)
Competitively priced, small-footprint system fits nicely into the budget and floor space at Inovata Foods
- Automation shines at Heinz
(Packaging World, May 2008)
At the Heinz Pocatello, ID, plant, Smart Ones frozen meals are run through a highly automated line that includes automatic depositing of a vegetable/rice mixture
- Equipment innovations bring new level of automation to packaging operations
(Food Manufacturing, November 2005)
Pack Expo Las Vegas to showcase latest machine innovations
- Mayor automatización en las operaciones de envasado
(El Empaque + Conversion, Septiembre 2005)
Para los empacadores con operaciones manuales, la tecnología robótica y los nuevos diseños en equipos hacen que hoy sea más fácil automatizar su maquinaria
- Precision filling, as requested
(Food Engineering, December 2004)
Growing demand for individual portions posed a specialized filling challenge to a Michigan copacker (Request Foods)
- Fill a need
(Refrigerated and Frozen Foods)
The Pasta Mill (Canada) automates to increase production speeds, decrease variance, and keep a growing business...growing
Designing a food filling line: Product is king
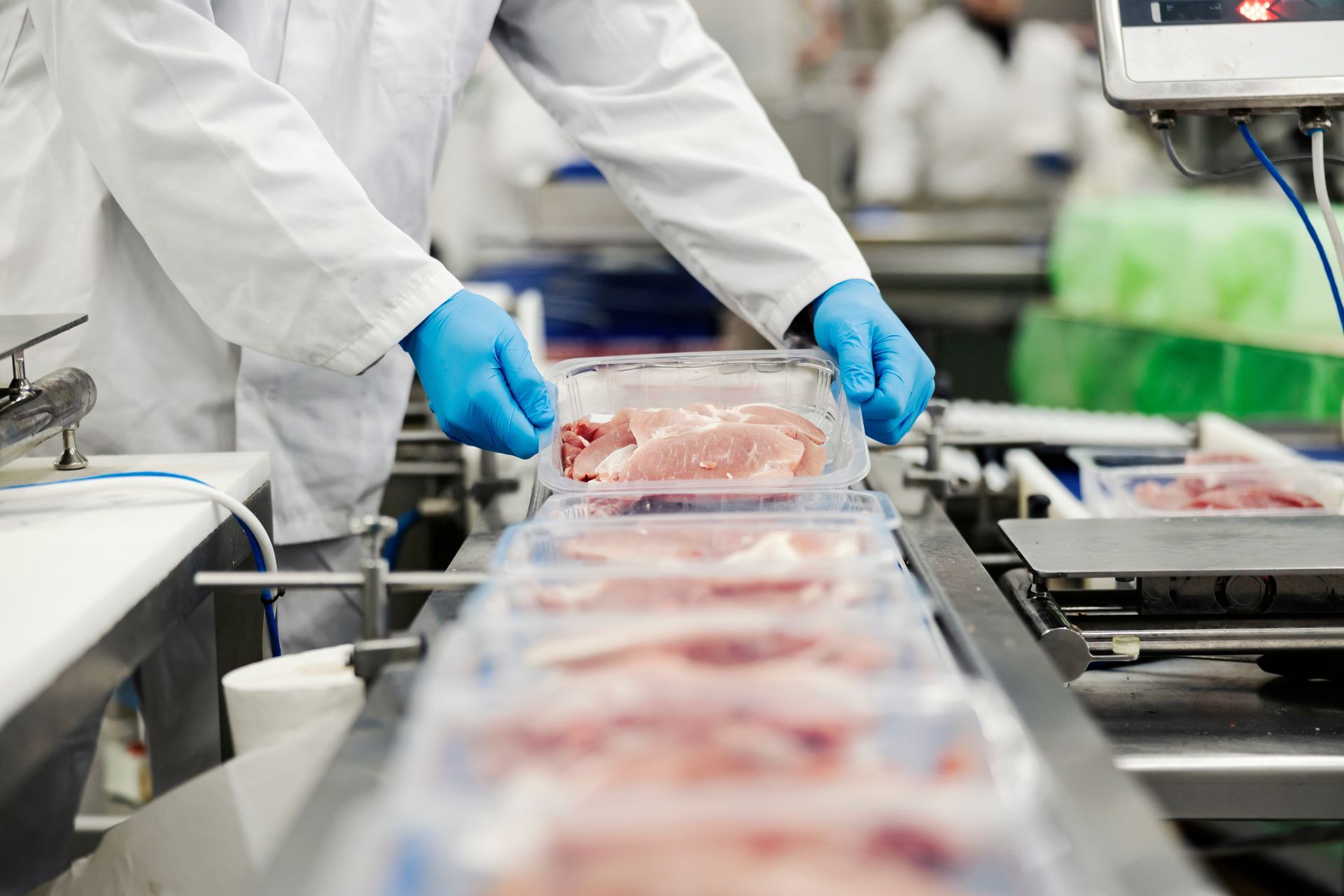
Food packaging plays a vital role in ensuring the safety and quality of the food we consume. To maintain high standards and prevent foodborne illnesses, the food packaging industry follows a set of regulations known as Current Good Manufacturing Practices (cGMP). In this article, we will delve into cGMP and explore its impact on preventing foodborne illness. We will also take an inside look at how cGMP is implemented on a food factory line, the role of food filling equipment in ensuring compliance, and discuss the future of cGMP in food packaging for strengthening food safety.
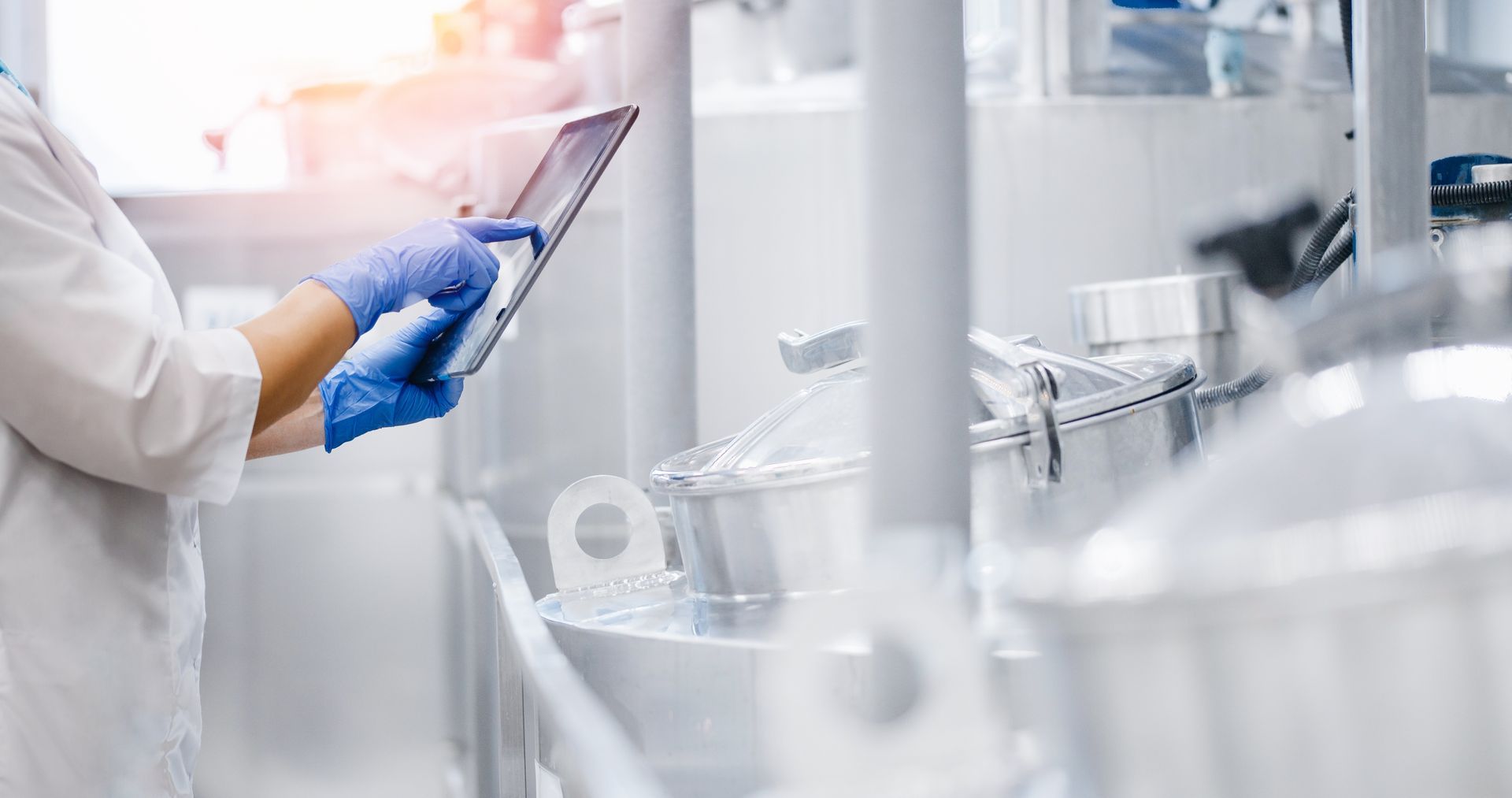
Current Good Manufacturing Practices Food safety is of utmost importance in the food industry, and several systems work together to prevent foodborne illnesses. This article explores the harmonization of Current Good Manufacturing Practices (cGMP), Hazard Analysis and Critical Control Points (HACCP), and Hazard Analysis and Risk-based Preventive Controls (HARPC) in ensuring food line safety. We will delve into the synergy between these systems, the role of critical control points, and their practical application in both automatic and manual counting devices. Additionally, we will discuss how cGMP, HACCP, and HARPC optimize automatic filling machines for enhanced food safety. This article is in our series on Current Good Manufacturing Practices. Read the first article here.
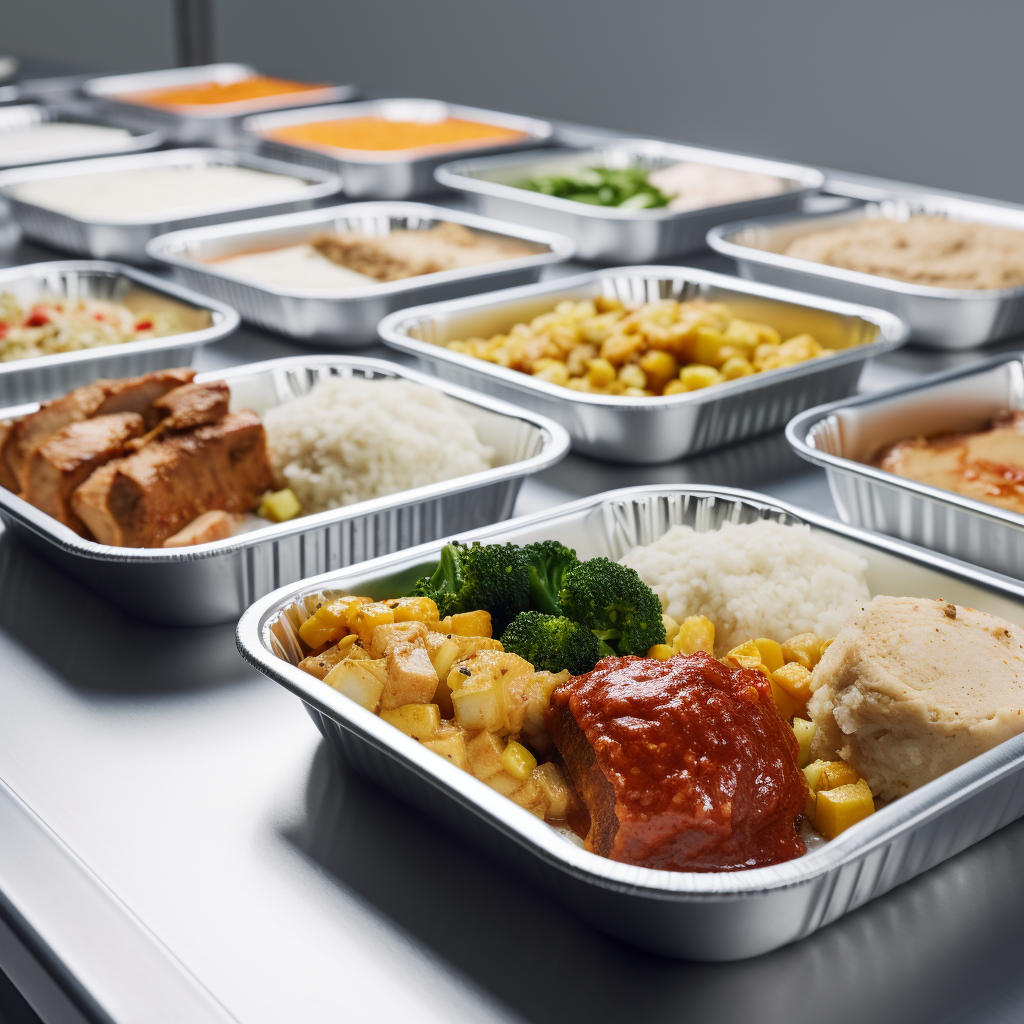
In this article, we explore the crucial role of Current Good Manufacturing Practices (cGMP) in ensuring food safety and preventing foodborne illnesses. We'll delve into the significance of hazard analysis and critical control points (HACCP) and how they contribute to mitigating risks. Additionally, we'll discuss the role of Hazard Analysis and Risk-based Preventative Controls (HARPC) in enhancing food safety measures. This is the first in a series of articles on Good Manufacturing Processes in Food Processing. In this article: Understanding the Importance of cGMP in Food Packaging How Hazard Analysis and Critical Control Points (HACCP) Prevent Foodborne Illness The Role of Hazard Analysis and Risk-based Preventative Controls (HARPC) in Food Safety Critical Control Points in Food Packaging The Intersection of cGMP, HACCP, and HARPC in Food Safety